2025 Heavy-Duty Truck Labor Guide
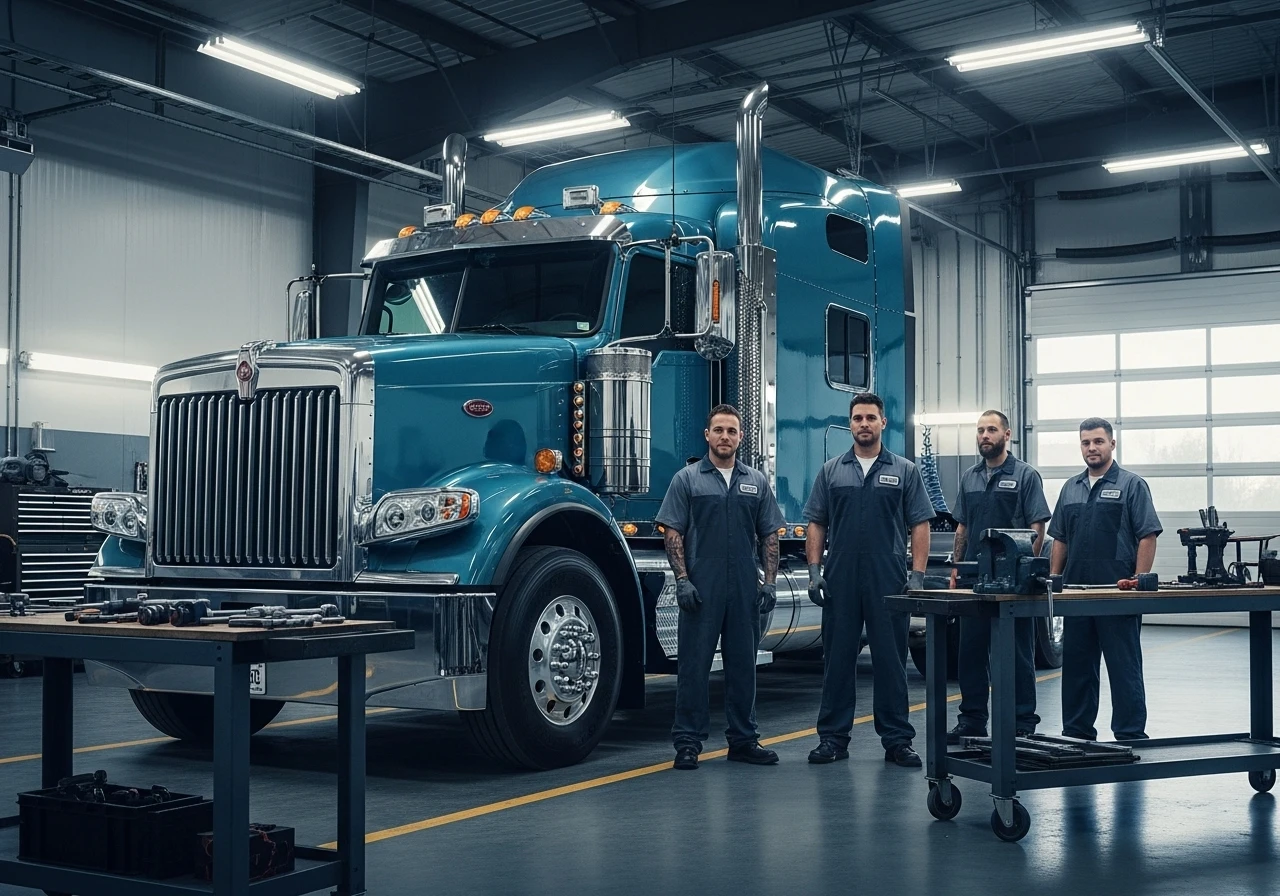
Accurate labor times and clear pricing are essential for a profitable heavy-duty repair business. The labor times in this guide combine information from recent surveys of fleets and dealerships with anonymous data from Easy Truck Shop (ETS) users. Record your shop's results in ETS to make your estimates more precise over time. We include average figures along with a "typical range" (about 20% above or below the average) to show how much times can vary between shops.
What Is a Heavy-Duty Truck Repair Labor Guide?
A labor guide provides the standard time a skilled technician typically needs to complete specific repairs. These guides use data from nationwide repair time studies, digital databases, real-world fleet information, and ongoing feedback from technicians. They help you create consistent quotes, train your staff, and justify your invoices.
How We Determine Labor Times
- What's Included: Labor times cover setup, teardown, and basic diagnostics for the repair.
- What's Excluded: Tasks like parts runs, administrative work, and moving vehicles between bays are not included. You should bill for these separately.
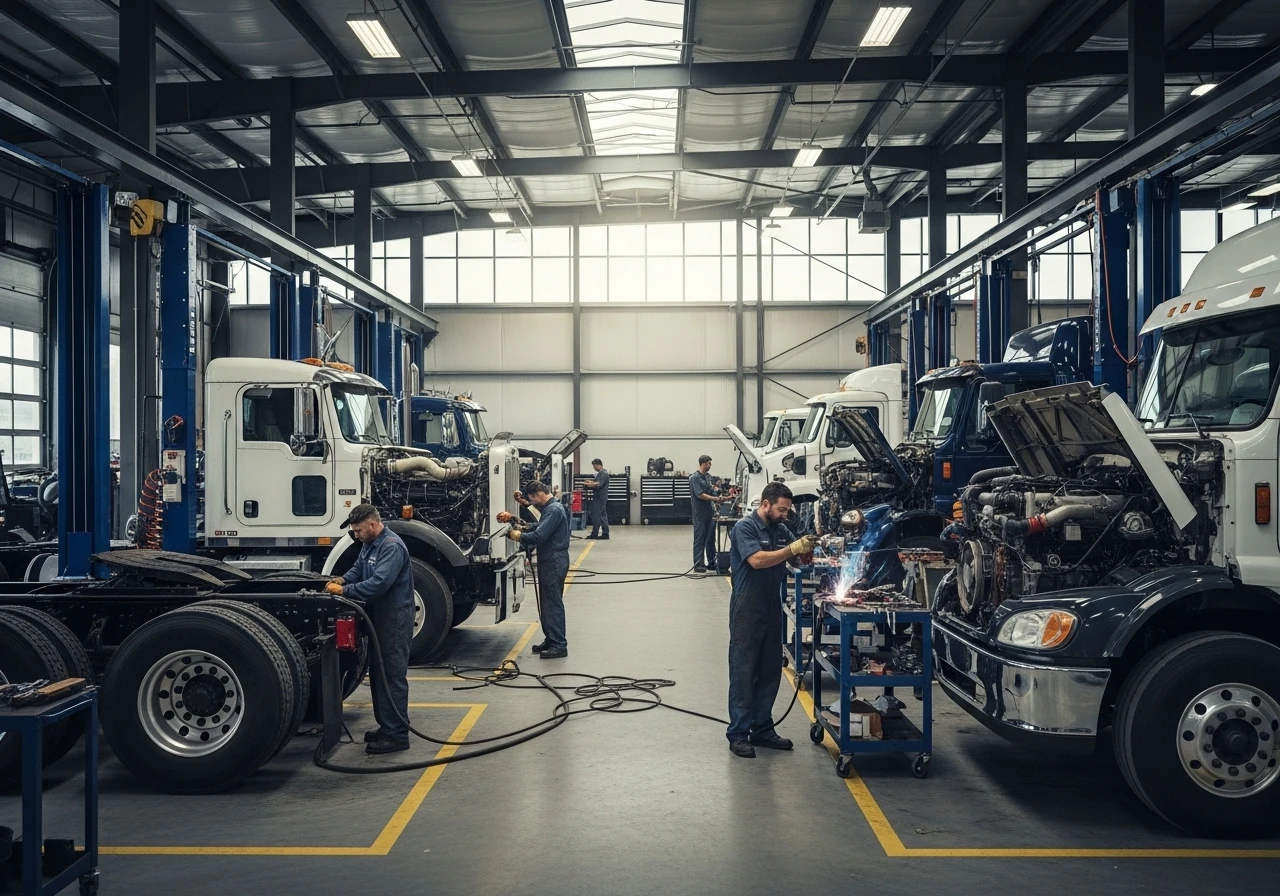
Real-World Labor Times for Semi-Trucks and Trailers
Start with these times, then adjust them to fit your specific tools, shop layout, and technician skill levels.
Suspension and Axle Labor Times
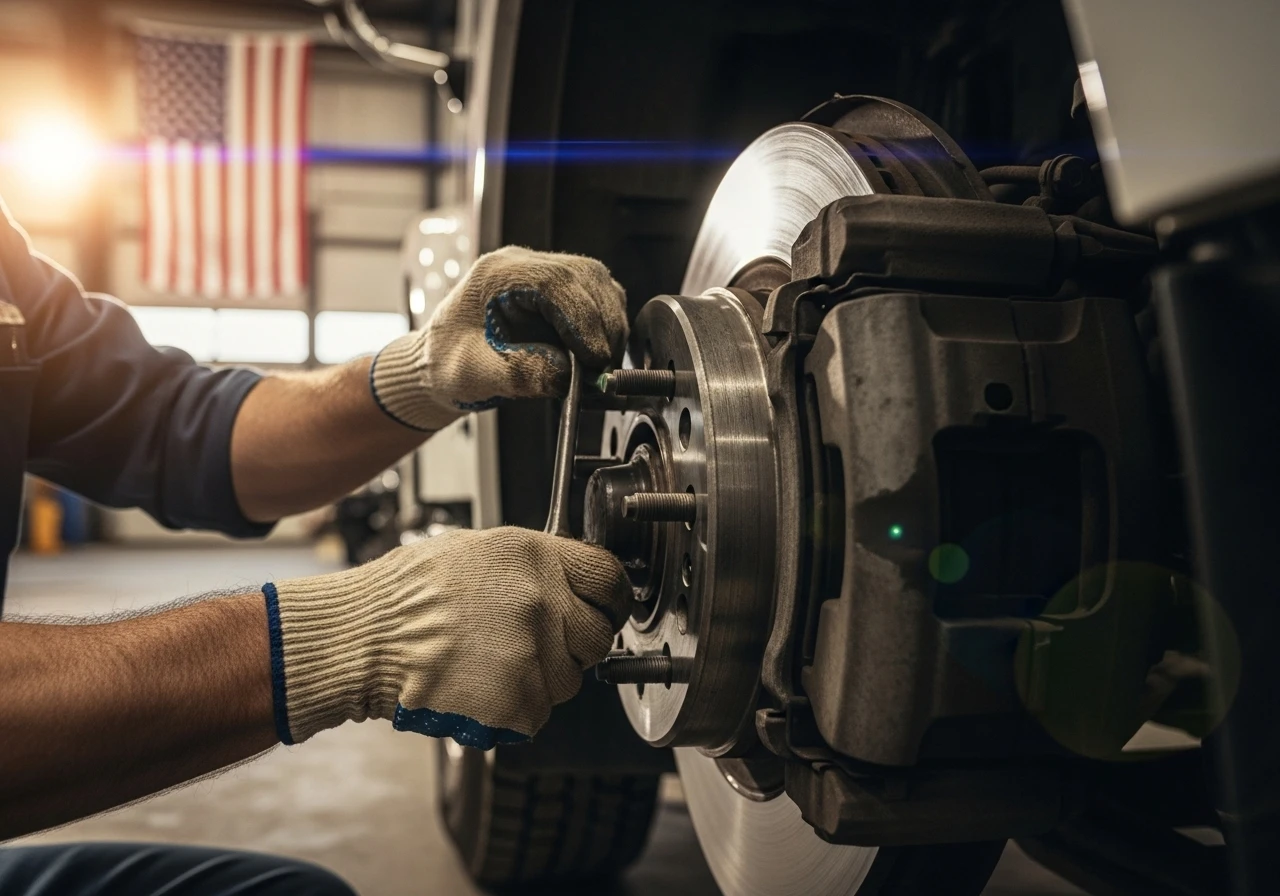
Brake and Undercarriage Labor Times
Landing Gear Labor Times
Electrical and Lighting Labor Times
Frame and Structural Labor Times
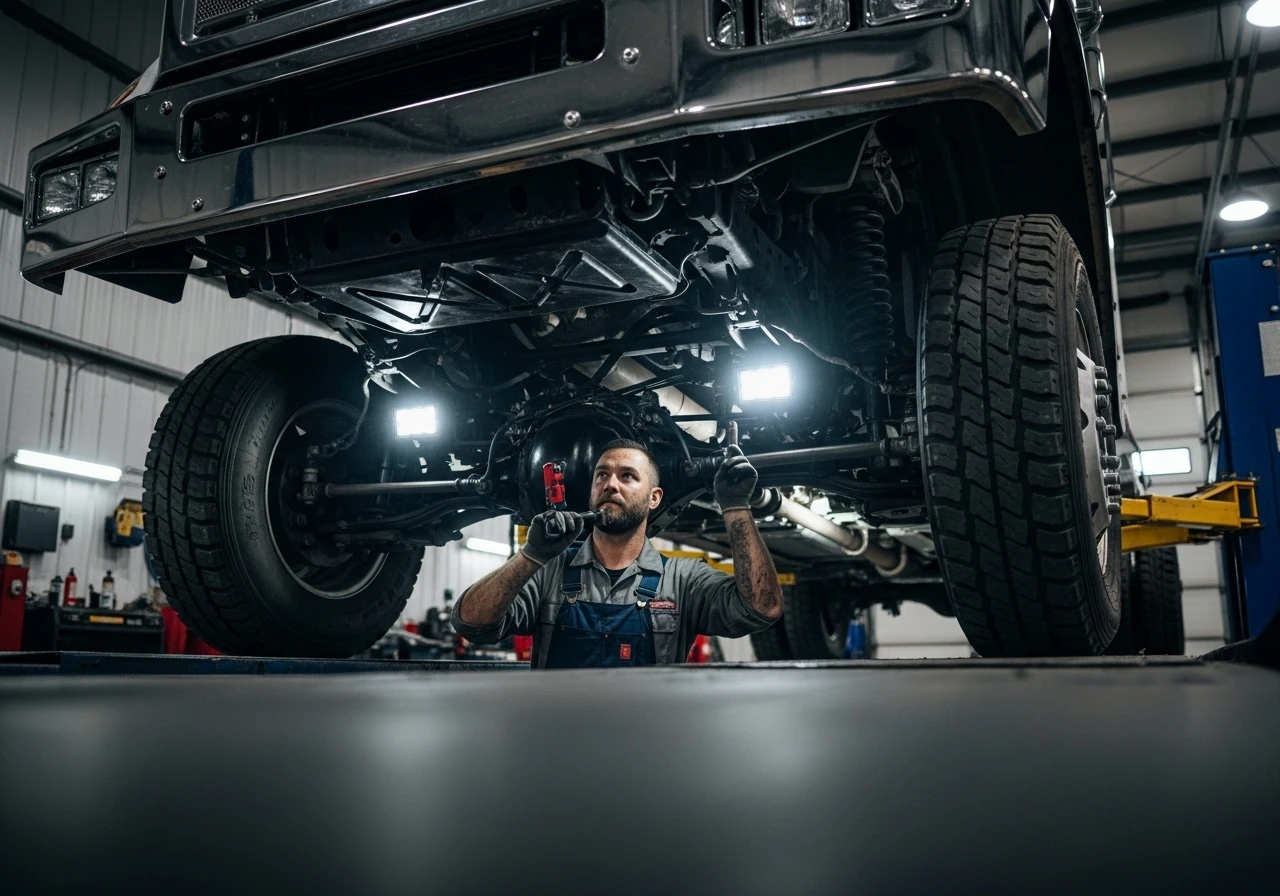
Floor Labor Times
Liftgate Labor Times
Common Heavy Duty Labor Times
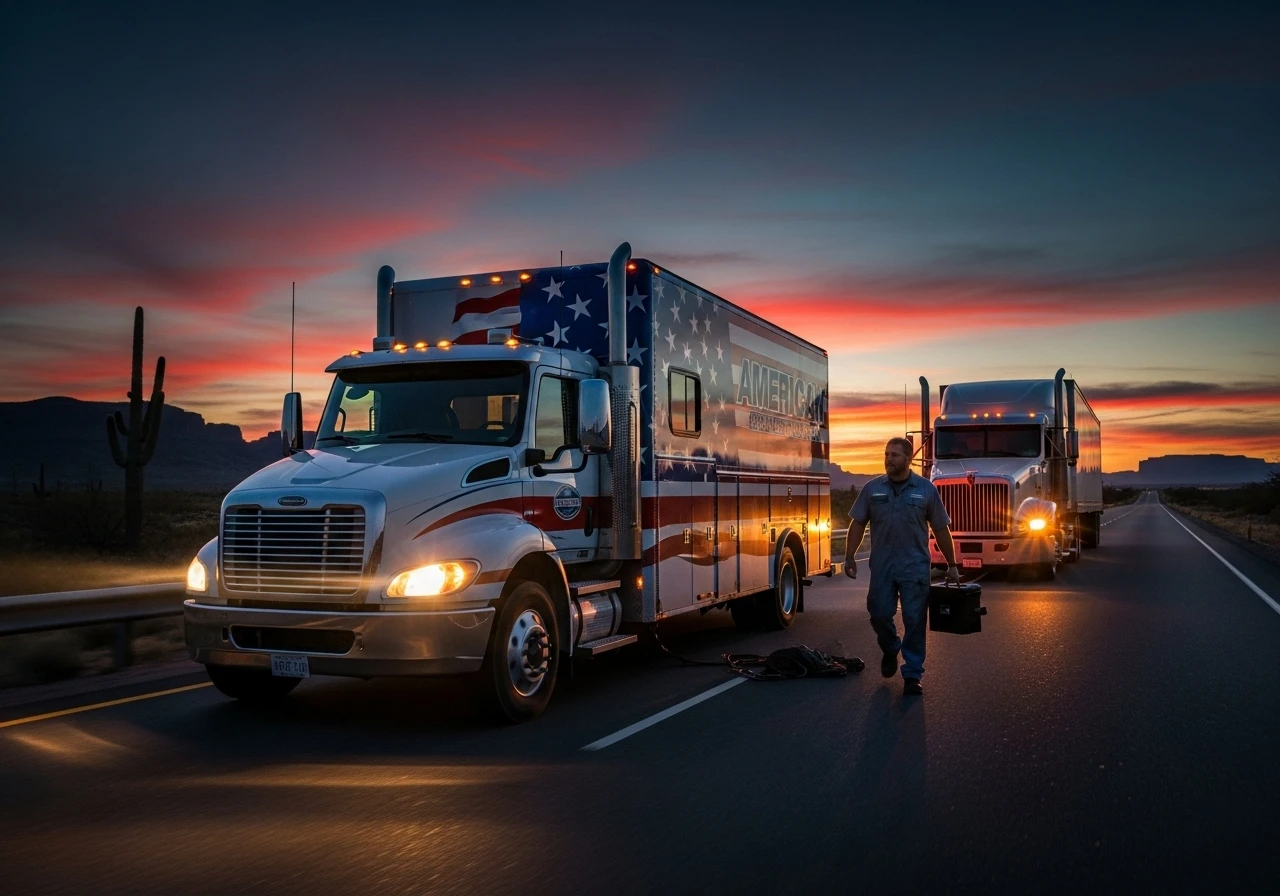
Regional Labor Rate Variances
The average shop rate is $134 per hour. Adjust this rate using these regional multipliers:
Industry Benchmarks and Trends
- Technician Pay: The average technician earns about $26 per hour. Certified master technicians often earn $38 or more. Keep entry-level wages competitive and offer clear paths for technicians to advance to master rates.
- Shop Size: A balanced dealership typically has about 18 technicians and 19 bays, which is roughly one bay per person. Having too many bays for your technicians wastes rent, while too few can cause bottlenecks.
- Profit Mix: On an $800 repair order, aim for a profit mix of 20% for labor, 25% for parts, 30% for overhead, and 25% for profit. If your overhead goes above 35% or your labor profit drops below 17%, you should adjust your prices or reduce costs.
- Pay Structure: About two-thirds of shops use a mix of hourly pay, flat-rate hours, and performance bonuses. This combination rewards speed without sacrificing quality.
- Mobile Service: Approximately 35% of shops charge about 1.25 times their in-bay rate for on-site repairs to cover travel time, fuel, and vehicle wear. Consider adding a call-out fee for very short jobs.
- Efficiency and Utilization: Top-performing shops bill more labor hours than their technicians actually work and keep technicians busy on billable jobs for at least 85% of each shift. Review both these metrics weekly and provide coaching to any technician who is not meeting targets.
Using Labor Guides for Shop Success
- Calibrate Your Estimates: Begin by using these average labor times, then fine-tune them using the actual time recorded from your ETS time cards.
- Coach Your Technicians: Compare each technician's actual performance to the guide's hours and provide coaching for those whose times vary significantly.
- Target Part Margins: Aim for a 45% gross profit margin on parts and add a 5-8% shop supply fee.
- Refresh Your Data: Update your labor times and rates quarterly or whenever you adopt new tools.
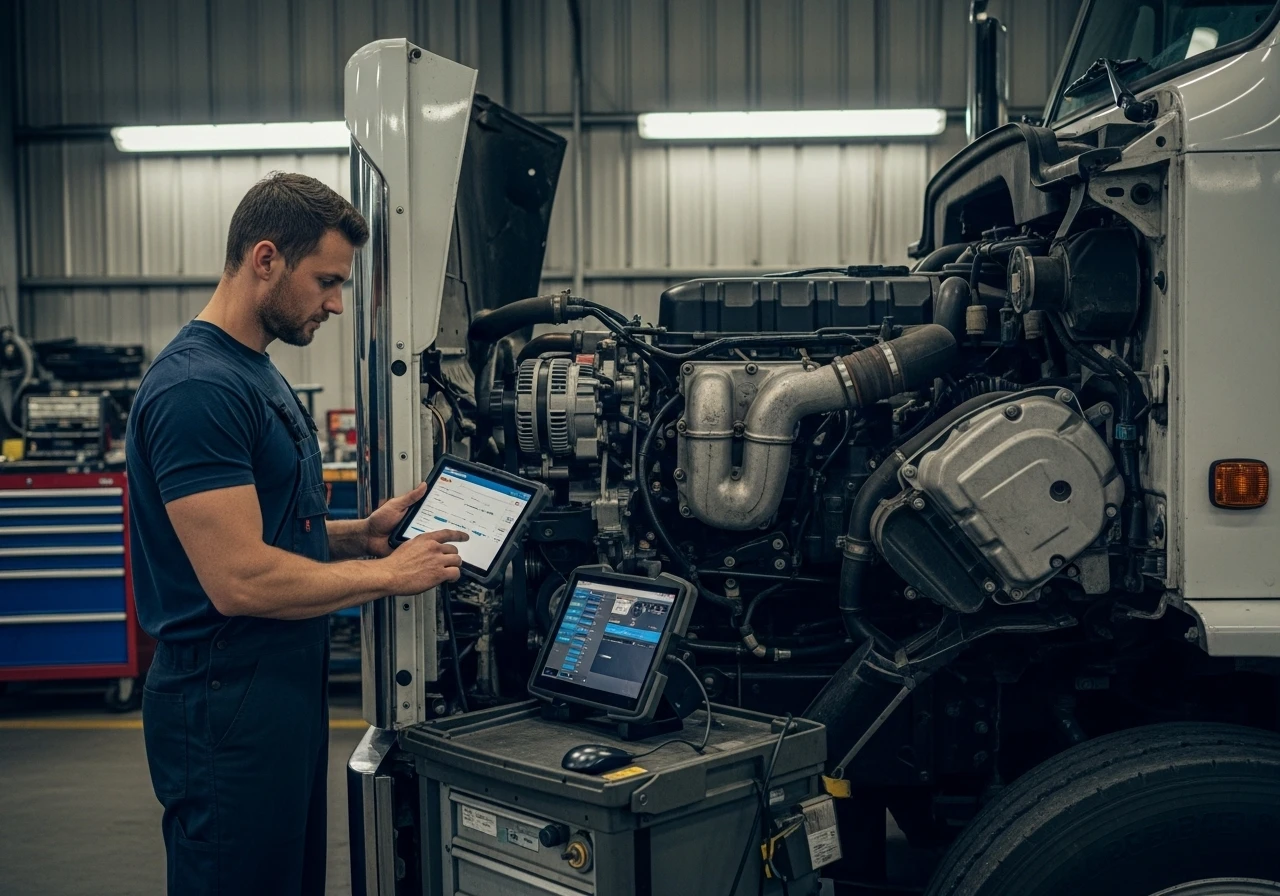
Building a Custom Labor Guide in Easy Truck Shop
Easy Truck Shop (ETS) does not come with a pre-loaded national database. Instead, its Service Types module lets you create a custom labor guide using your own shop's data:
- Create Service Categories: Set up categories for tasks like diagnosis, repair, replacement, and maintenance.
- Enter Standard Times: Assign a standard hour for each task.
- Track Real-Time Performance: Technicians clock in and out of tasks in real time.
- Review Performance Reports: ETS provides variance reports that show you how actual times compare to your standards, helping you refine your estimates.
- Adjust Anytime: You can instantly edit any labor line, and these updates will apply to future quotes.
Calibrating Labor Times for Your Shop
While national labor time averages are a good starting point, adjusting these times to your shop is crucial for accurate quotes and maximum profit. Calibration means comparing your shop’s actual repair times against the guide and adjusting your standards.
Step-by-Step Calibration Process:
- Start with the Guide’s Averages: Use the published average labor times as your initial estimates for common jobs.
- Track Actual Labor Hours: Use your shop management system to record the exact hours technicians spend on each repair task.
- Organize Tasks Clearly: Break down repairs into specific categories like diagnosis, repair, replacement, and maintenance for consistent tracking.
- Analyze Variances: Regularly check reports that compare actual hours to the guide’s standard hours. This helps you find where your shop performs differently.
- Investigate Outliers: If a technician consistently takes more or less time than the standard, find out why. It could be due to skill levels, specific tools, or workflow.
- Adjust Your Labor Standards: Update your internal labor times based on your shop’s data. This ensures your future estimates are more precise.
- Review Periodically: Reassess and update your calibrated labor times every quarter. This accounts for new tools, technician skills, and changes in truck technology.
By following this process, your labor guide becomes a customized tool reflecting your shop’s real performance, improving quote accuracy and financial results.
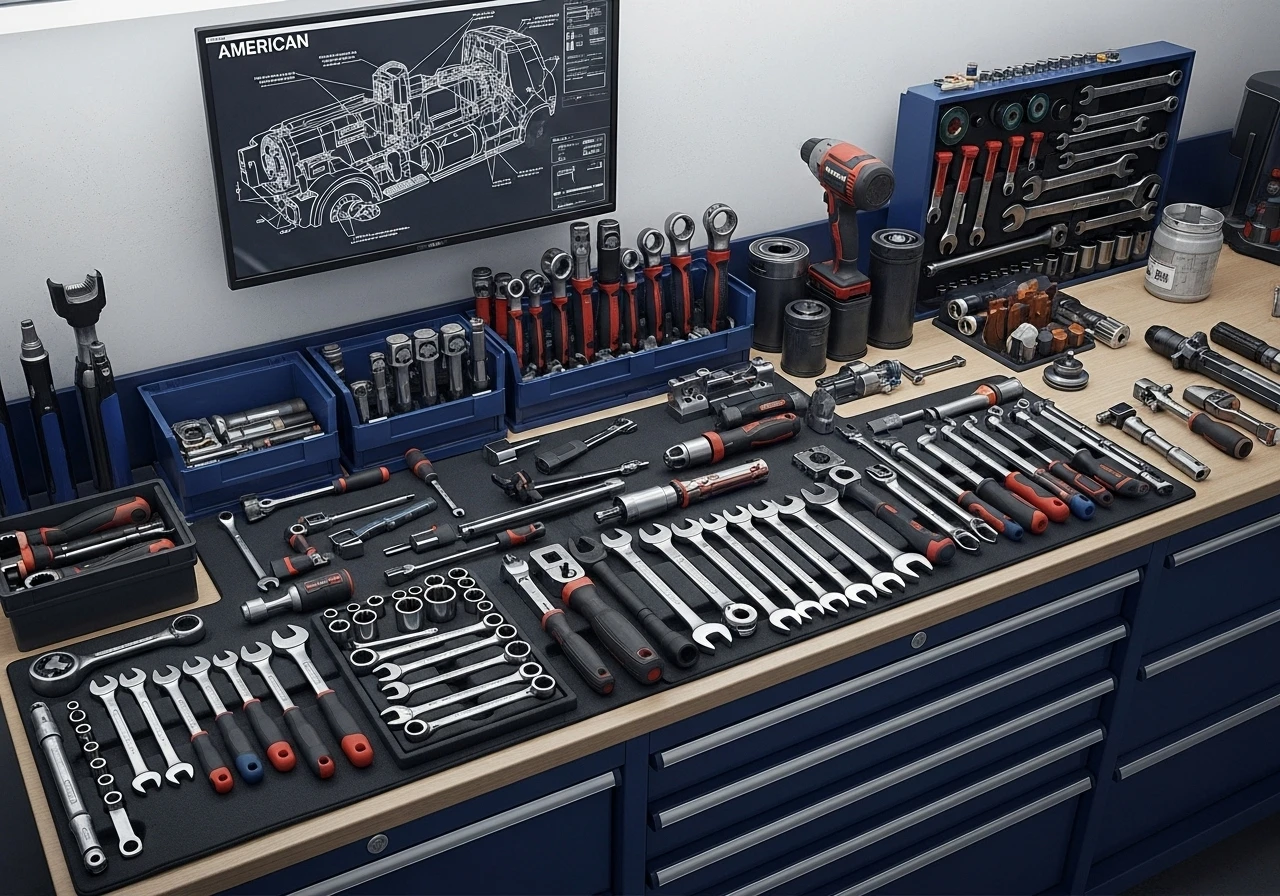
Common Pitfalls in Estimating Labor Times and How to Avoid Them
Accurate labor estimates and pricing are difficult. Many shops make common mistakes that reduce profits or customer satisfaction. Learning about these pitfalls can help you avoid costly errors.
- Using Generic Averages Without Adjustment: Applying national labor times without customizing them for your shop’s conditions can lead to wrong estimates. Avoid this by tracking your own data and tailoring labor times to your shop.
- Not Billing for Excluded Tasks: Standard labor times often do not include tasks like parts runs, administrative work, or moving vehicles. Forgetting to bill for these cuts into your profit. Make sure you identify and invoice these tasks separately.
- Infrequent Rate and Time Updates: If you do not update your labor rates and times regularly, they can become outdated due to market changes or higher costs. Review and update your labor rates and calibrated times at least quarterly to stay competitive and profitable.
- Ignoring Technician Efficiency and Utilization: Not tracking how efficiently technicians work (hours billed vs. hours worked) and how much time they spend on billable jobs can hide productivity issues. Track both efficiency and utilization to find and fix performance gaps.
- Charging the Same Rate for Mobile Repairs: Mobile repairs have extra costs like travel and fuel. Charging the same hourly rate as in-shop work means you are not covering these expenses. Use higher rates or call-out fees for mobile service to cover these costs.
- Neglecting Profit Mix and Overhead Control: Not analyzing your shop’s profit mix and overhead can lead to pricing that does not cover costs. Aim for a balanced profit distribution and adjust prices or reduce overhead if your labor or profit margins fall too low.
Frequently Asked Questions
Why do my repair times differ from this guide?
These times are national averages. Your shop's efficiency, your technicians' experience, your tools, and the truck's specific condition will cause differences. Use a shop management system to track your own data and adjust these baselines for your shop.
How often should I update my shop's labor rates?
You should review your labor rates at least once a year, but reviewing them quarterly is better to keep up with market changes and rising costs. While 45% of shops review annually, more frequent checks ensure you do not miss potential revenue.
What is included in a standard labor time?
Standard labor times generally cover the main repair process: setup, teardown, the repair itself, and common diagnostics directly related to the job.
What is not included and should be billed separately?
Tasks like running for parts, long or unrelated diagnostic time, administrative work, and moving vehicles between bays are usually not included. You should bill for these separately.
Should I charge more for mobile repairs?
Yes. Most shops charge a higher rate for mobile service, often around 1.25 times their in-bay rate. This covers travel time, fuel, and wear on your service vehicle. Many also add a flat call-out or trip fee, especially for short jobs.
How are these labor times determined?
These labor times combine data from nationwide studies on standard repair times, digital databases, actual fleet maintenance records, and anonymous information from thousands of repair shops using ETS.
What is a good target for technician efficiency and utilization?
Top shops aim for technician utilization of at least 85%. This means technicians are actively working on billable jobs for most of their shift. Efficiency, which compares hours billed to hours worked, can go over 100% if technicians finish jobs faster than the standard time or work on multiple jobs effectively.
How can I create a custom labor guide for my shop?
Use a system like Easy Truck Shop to track the actual time your technicians spend on various jobs. By setting up service categories and having technicians clock in and out of specific tasks, the system can provide variance reports. This allows you to refine your estimates and build a labor guide based on your own shop's data.
Related Articles
Discover more articles on related topics to expand your knowledge.
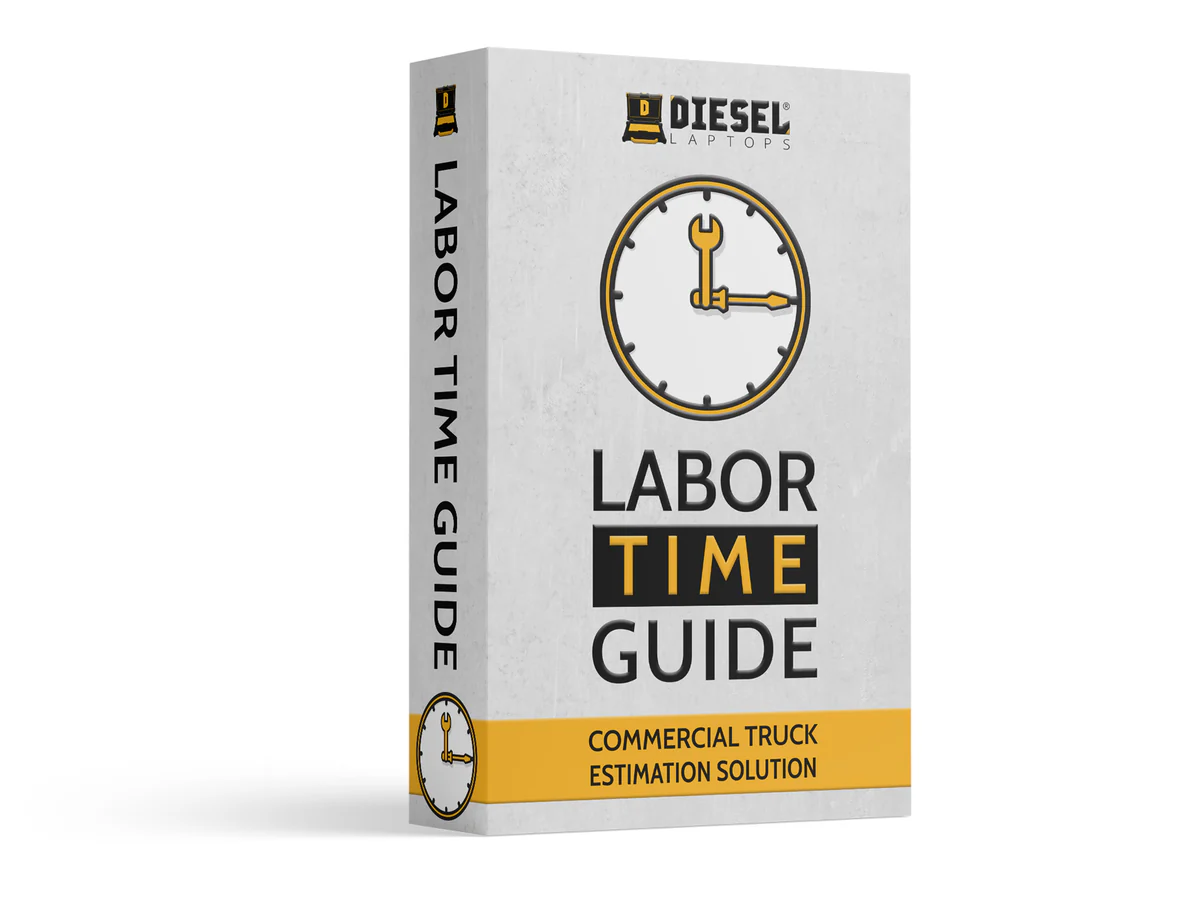
Heavy Duty Truck Repair Labor Guide With Easy Truck Shop
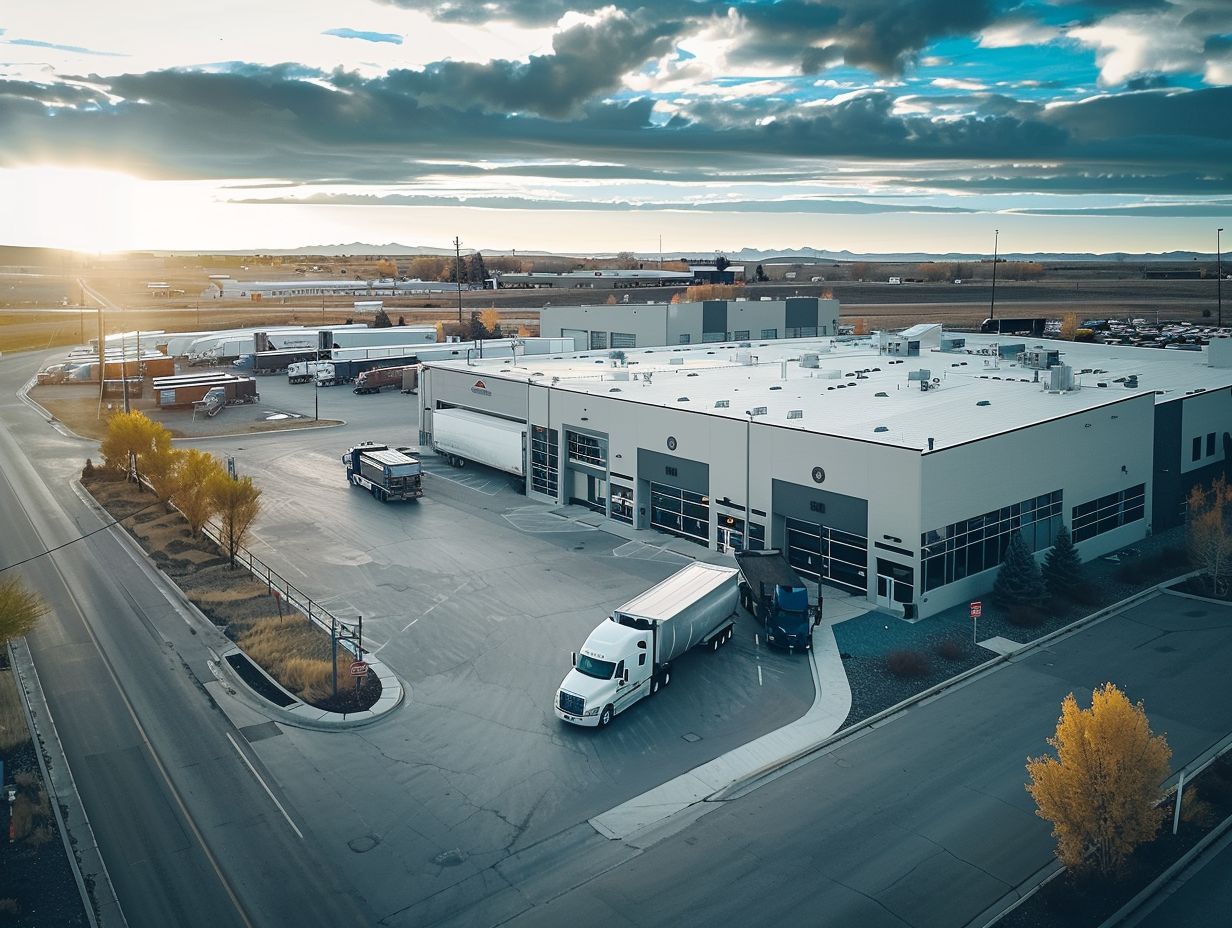
21 Pro Tips on How to Run a Successful Mechanic Shop
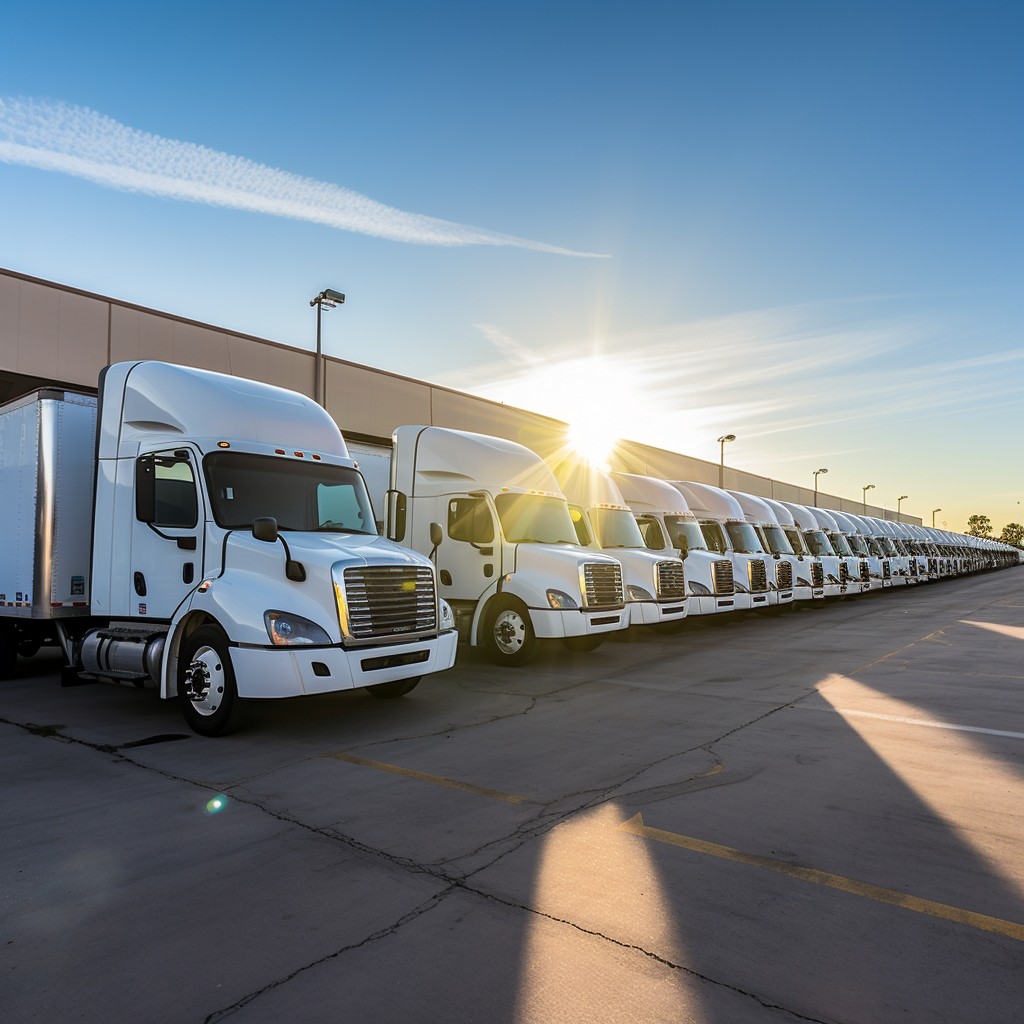